Best Practices for Integrating Quality Assurance into Your Six Sigma Projects
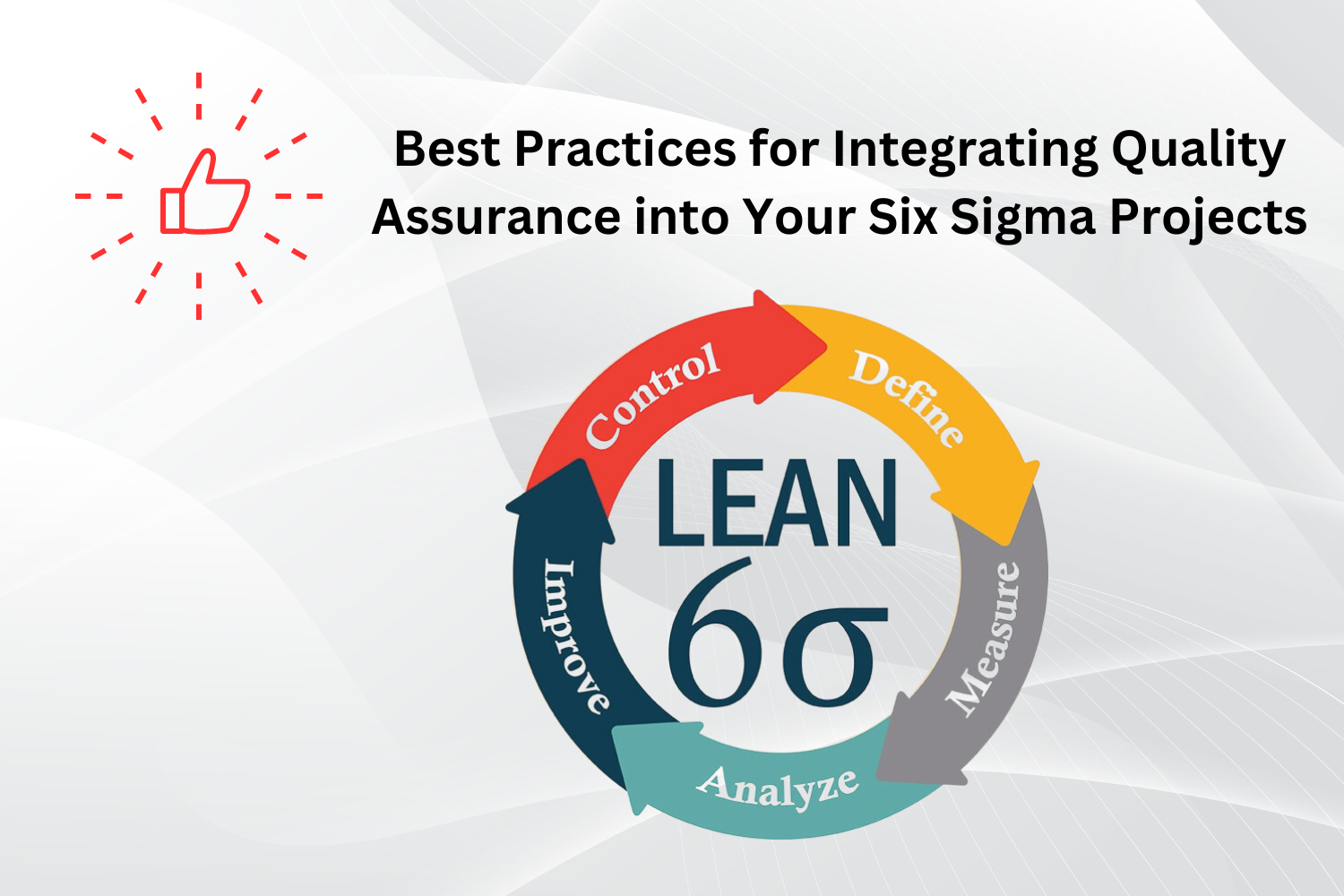
The incorporation of Quality Assurance (QA) into Six Sigma is a strategic necessity for organisations striving for unparalleled excellence. Integration of Quality Assurance in Six Sigma guarantees a comprehensive approach to process optimisation, highlighting the necessity of accuracy, ongoing development, and long-term success. Leveraging the advantages of Six Sigma Training Online becomes critical as organisations go on this integrated path, equipping teams with the skills and expertise required for the successful application of both approaches.
Table Of Contents
- Align Quality Assurance Objectives with Six Sigma Goals
- Establish Clear Quality Standards
- Integrate Quality Metrics into Six Sigma Framework
- Implement Robust Quality Control Processes
- Adopt Cross-Functional Collaboration
- Leverage Quality Assurance in Root Cause Analysis
- Utilise Quality Assurance Tools for Continuous Monitoring
- Prioritise Training and Development
- Establish a Feedback Loop between QA and Six Sigma Teams
- Emphasise a Culture of Continuous Improvement
- Conclusion
Align Quality Assurance Objectives with Six Sigma Goals
The overarching goals of Six Sigma must be aligned with the objectives of Quality Assurance to form a coherent approach. Clearly state the contributions that quality assurance procedures will make to each DMAIC (Define, Measure, Analyse, Improve, Control) phase of the Six framework. This alignment makes sure that both approaches complement one another to improve processes and produce the intended results.
Establish Clear Quality Standards
Clearly state and disseminate the organisation’s quality requirements. These requirements ought to be quantifiable, reachable, and consistent with what customers anticipate. Maintaining these standards should be the focus of quality assurance initiatives since they serve as a benchmark for Sigma projects to successfully find and eradicate deviations.
Integrate Quality Metrics into Six Sigma Framework
The foundation of both Six Sigma and Quality Assurance is quality metrics. Choose industry-relevant key performance indicators (KPIs) and incorporate them into the Six Sigma DMAIC framework. This connection makes sure that information produced by Q.A. procedures is used to inform decisions made during Six Sigma projects.
Implement Robust Quality Control Processes
To find and fix errors, Quality Assurance depends on strict quality control procedures. Incorporate these procedures into the Six Sigma Analyse and Improve stages, emphasising the application of efficient corrective and preventive measures as well as root cause analysis. Sturdy quality control procedures have a major role in lowering variances and faults.
Adopt Cross-Functional Collaboration
Encourage a collaborative culture between Sigma and Quality Assurance teams. Create lines of communication that allow information, knowledge, and insights to flow easily back and forth. By utilising the many views and abilities inside the company, cross-functional collaboration guarantees that all stakeholders contribute to the success of Sigma projects.
Leverage Quality Assurance in Root Cause Analysis
The fundamental goal of Quality Assurance procedures is to locate and resolve problem causes. Include QA techniques in the Six Sigma Analyse stage, placing special emphasis on a comprehensive analysis of the root causes of process deviations. This combination improves the accuracy with which Sigma professionals identify and remove underlying causes.
Utilise Quality Assurance Tools for Continuous Monitoring
In Six Sigma projects, quality assurance techniques like failure mode and effects analysis (FMEA) and statistical process control charts are invaluable resources. Incorporate these instruments into the Six Sigma Control stage to ensure ongoing process observation. This guarantees the long-term sustainability of the gains achieved throughout the Sigma project, which promotes success in the long run.
Prioritise Training and Development
Fund training and development initiatives to provide staff members with the know-how and abilities needed to successfully integrate Sigma and quality assurance principles. A staff that is knowledgeable about both approaches is more suited to support efforts for process improvement and promote the success of the company.
Establish a Feedback Loop between QA and Six Sigma Teams
Establish a feedback loop to help the Sigma and QA teams communicate with each other. Share your thoughts, successes, and lessons learned regularly. This cooperative method encourages ongoing development by enabling both teams to modify their tactics in response to input and new developments.
Emphasise a Culture of Continuous Improvement
The idea of continuous improvement is the foundation of both Six Sigma and Quality Assurance. Encourage this way of thinking throughout the culture of the company. Motivate staff members to proactively spot areas that could be improved to create an atmosphere where Sigma and QA are integrated into regular operations.
Conclusion
Including Quality Assurance in Six Sigma initiatives is not only a strategic decision; it creates a potent synergy that drives businesses toward unmatched success and long-lasting quality. Through the establishment of unambiguous standards, integration of quality indicators, alignment of objectives, and promotion of cross-functional collaboration, organisations can effectively leverage the combined potency of these techniques.
Strong quality assurance procedures, the use of QA tools, and an ongoing feedback loop guarantee that the integration is a continuing commitment to excellence rather than a one-time endeavour. Businesses position themselves to navigate the complexities of the business landscape with a robust toolkit that combines accuracy, data-driven decision-making, and an unwavering focus on continuous improvement as they adopt best practices for integrating Quality Assurance into their Six Sigma projects.
More Contents :
Red Cedar Message board:
darez diggs
andreaabelix
bluelite usps
esmé bibi ayoade